d. Development. The exposed plate is immersed in water for a minute or two. It is necessary to shake the frame and wait until the unexposed part has absorbed moisture and swell. Rinse with water. Development should be completed as soon as possible. Sometimes with 3.5 ~ 5.5kg/cm2 spray gun, water development from both sides. Due to the different types of photosensitive liquids, some are easily developed and some are not easily developed, but in any case, the unexposed areas must be completely dissolved away. When the pattern is fine, it is necessary to use a 8 to 10 times magnifying glass to check if the subtle part is completely empty. After developing, use a sponge or hair dryer to quickly remove the moisture and dry.
Due to the difference in the kind of the photosensitive liquid, warm water development is applied to a polyvinyl alcohol emulsion film having a high degree of polymerization and a solvent-resistant emulsion film.
For nylon film, use industrial alcohol to develop it. After the finest image can be fully displayed, check it carefully. All the images can be clearly displayed and rinsed with water. Developed alcohol can be retained and used multiple times.
Due to the different nature of the photosensitive material, the plate-making requirements and the development requirements are also different, and the plate-making methods and developing methods commonly used for different photosensitive materials are listed in Table 2-33.
See Blue Table 2 Different Methods for Making and Developing Photosensitive Materials
The principle of control of the degree of development is: under the premise of being transparent, the shorter the time, the better. If the time is too long, the film will suffer from wet expansion and affect the clarity of the image; if the time is too short, the development will not be complete, and there will be ignorance, blockage of the mesh, and waste. Mongol is a very thin layer of photosensitive adhesive residue, easy to appear in the details of the image, highly transparent, difficult to distinguish with the water film, often mistaken for clear. In order to facilitate observation, light developing water tank can be used; self-made light observation bench can also be used.
e. Drying. The developed screen plate should be placed in a dust-free dry box and blown with warm air. The screen-type drying box is a plate-making equipment for low-temperature drying after screen cleaning and coating of photo-sensitive adhesive. Drying temperature can generally be controlled at 40 ± 5 °C.
Screen drying box can be divided into vertical and horizontal two.
The drying box should be equipped with an automatic temperature control system or timing device, and keep the inside of the box clean.
The vertical drying oven has a small footprint and is suitable for screen plates with large areas and low precision requirements.
Horizontal drying oven covers a large area and is suitable for screen plates with small area and high precision.
Two kinds of drying boxes are multi-row and multi-layer, which can ensure that multiple screen plates are dried simultaneously.
When drying, the moisture on the surface of the screen should be blown off in advance so as to prevent the moisture from flowing down the surface of the screen to produce residual adhesive, which affects the sharpness of the line edges. If the hardener is used to treat the layout, it can be done after the water is washed. Pay attention to uniform cloth flow.
After the screen is dry, it can be checked on the translucent inspection table to see if there are any marks such as blisters, etc., and the edge of the line can be trimmed with glue.
f. Reinforcement and correction of the film. Before or after the printing plate is dried, in order to strengthen the printing plate and improve the water resistance and the solvent resistance, an anhydrous dilute chromate solution may be applied. However, from the perspective of preventing public hazards, it is not appropriate to use chromic acid-based drugs. Recently, there have been marketed relatively small hardeners for sale.
Secondly, in order to block the pinholes or openings that should not be on the plate, block the blockage with a blocking liquid or a photosensitive liquid for plate making.
In the printing process, the ink and ink leakage may sometimes occur at the junction of the net and the frame. In particular, when the adhesive is fixed, the ink leakage phenomenon is more likely to occur. In this case, the ink should be shielded with an appropriate material to prevent the ink solvent from leaking out of contact with the adhesive.
In order to enhance the imprint resistance of the printing plate, the revised printing plate can be exposed again (secondary light). The length of time depends on the light intensity. The film remaining on the screen can be more sturdy by being exposed to ultraviolet rays again. Resist printing.
Hard film is divided into two methods: physical hardening and chemical hardening:
The chemical hardening method is a method of treating a prepared template with a chemical agent to change the hydrophilic group (such as -OH, -COOH, -NH3, etc.) or increase the degree of polymerization and the degree of crosslinking, thereby enhancing the water resistance of the entire film. Sex. For example, the hydrophilic group -NH3 of gelatin in the indirect template can be treated with the following hardener:
Diethylene glycol 1 part
Formaldehyde water solution (40%) 2 parts
12 parts of water
When the indirect stencil is pasted on the screen, the screen is immediately wetted with a sclerosing solution for 2 to 3 minutes, and then the absorbent paper is pressed for compaction. After 12 hours, it can be used. During the treatment, the formaldehyde in the firming solution reacts with the amino group of gelatin as follows:
R-NH2+HCHO→R-N=CH2+H2O
The hydrophilic group is bound.
A three-dimensional network structure enhances the resistance.
Synthesizes chrome glue, diazo glue and photosensitive resin glue made of water-soluble macromolecules. Their treatment methods are basically the same, that is to say, the firm liquid is applied on both sides of the stencil and placed horizontally. After being naturally dried, it is placed in a 50-60°C oven for drying for 0.5-1.0 hours, or used after being naturally dried for one day.
The physical hardening method is actually coated with a layer of water-resistant protective film on one or both sides of the template to enhance water resistance. There are two kinds of processes - pre-painting and post-painting.
The pre-painting process is as follows: screen pre-treatment → drying → applying vinyl chloride rubber → drying → sanding → rinsing → drying → photoresist coating → drying → printing → development → drying → repairing with photosensitive adhesive → Retouch Partially Exposure → Wipe off the paint on the image with butyl acetate.
After the painting method of the process: screen pretreatment → drying → coating photosensitive adhesive → drying → printing → development → drying → sealing network and revision → printing surface scraping and image part paint removal → drying → scraping ink Scraper and image parts are removed from the paint and dried.
Removing the paint requires removing only the paint film from the image area, and the paint film on the surface of the pattern cannot be removed. It is best to suck it out with a suction machine, or use a cloth with a suitable solvent and wipe back the paint film from the back side until it is completely removed. Comparison of the two methods of painting can be seen: pre-painting method, plate making faster, screen version is easy to regenerate; post-paint method plate making cycle longer, but the template resistance is good, suitable for mass production.
The physical hardening method is not suitable for tasks with a mesh size of more than 220 mesh/inch. The chemical hardening process is simple, but it is difficult to remove the stencil after hardening.
g. Edge sealing. In order to protect the cleanliness of the adhesive net frame, facilitate the regeneration of the frame, and prevent the ink solvent from corroding and affect the adhesive force, it is necessary to tape the inside of the frame and the adhesive mesh surface, as shown in Fig. 2-116. Solvent-resistant coatings may also be used. Seal the area.
Figure 2-116 Screen Sealing Method
Wing Kam Packaging Co.,Ltd. was established in 2001, we are manufacturer and support custom design. We specialize in this Foldable Box Packaging. Our value message is "QUALITY IS OUR LIVE, WITHOUT QUALITY, WITHOUT US." If you order this Foldable Box Packaging from us, YOUR BUSINESS WILL BE SAFE, YOUR MONEY WILL BE SAFE, YOUR PRODUCT OUT LOOK WILL BE GORGEOUS.We also provide flower plastic container.
Item |
Foldable Box Packaging |
Dimension |
Customized |
Material |
PVC, PET |
Thickness |
0.2mm to 1mm |
Cardboard Insert |
Yes, Customized |
MOQ |
3000pcs |
Sample order |
Welcome & acceptable |
Product Pictures Show:
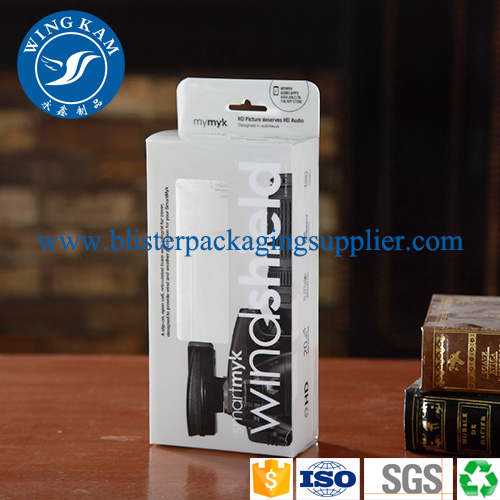
Welcome to order Foldable Box Packaging.
Any questions please contact us freely.
Foldable Box Packaging
Triangle Foldable Boxes Packaging,Plastic Foldable Box Packaging,Magnetic Foldable Paper Packaging Box,Cardboard Foldable Box Packaging
Shenzhen City Wing Kam Packaging Products Co., Ltd. , http://www.blisterpackagingsupplier.com